炭素鋼鋼管 炭素鋼シームレス鋼管 炭素鋼シームレス鋼管
説明
シームレス鋼管は、固体の丸い鋼の「ビレット」から作られ、鋼が中空の管に成形されるまで、加熱され、型枠上で押したり引っ張られたりします。その後、シームレス パイプは、外径 1/8 インチから 32 インチまでの寸法と肉厚仕様に仕上げられます。炭素鋼継目無鋼管・チューブ 炭素鋼は鉄と炭素からなる合金です。鋼中の炭素の割合は、炭素鋼の硬度、弾性の強さ、延性に影響します。シームレス炭素鋼パイプまたは固体鋼インゴットは、穴を通して毛細管から作られ、その後、熱間圧延、冷間圧延または冷間圧延が行われます。中国の鉄鋼産業において継目無炭素鋼鋼管は重要な位置を占めています。継目無炭素鋼管材料は丸管であり、パイプ切断機の初期段階で長さ約 1 m のブランクを切断し、ベルトコンベア加熱炉によって送られます。ビレットは約1200℃の加熱炉に投入されます。燃料は水素またはアセチレンです。炉の温度管理が重要な問題です。空気圧で機械を打ち抜くように丸いチューブが出てきました。一般的により一般的なパンチはテーパーロール穿孔機で、パンチは生産効率が高く、製品品質が高く、穴の直径が大きく、さまざまな鋼を摩耗できます。穿孔、丸管は 3 ロールクロス圧延、圧延または押出で行われます。サイジング後、チューブを絞り出します。高速回転コーンによるサイジングによりビレットに穴をあけ、チューブを形成します。パイプ径をサイジングミルで測定し、ドリル径の長さを決定します。パイプがサイジングを通って冷却塔に流入した後、水スプレーによって冷却され、冷却後の鋼は真っ直ぐになるはずです。スチールベルトは、内部試験のために矯正金属試験機(または圧力試験)によって送られた後。パイプ内部に亀裂が入ったり、気泡が発生したりする場合は、その他の問題が検出されます。パイプの後も厳格な品質管理を経て手作業で選別されます。鋼材の品質、スプレー塗料の使用番号、仕様、製造ロット番号。クレーンで倉庫に入ります。
継目無管の肉厚
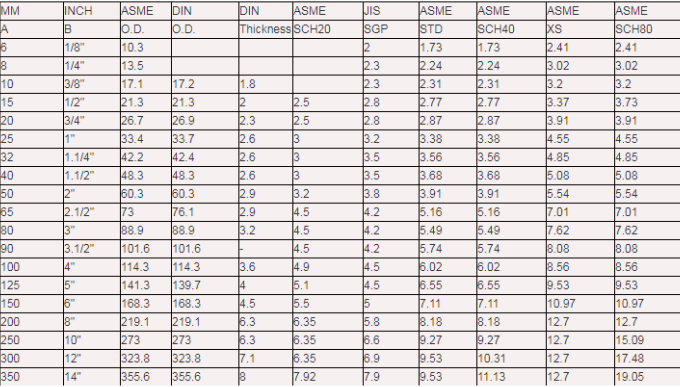
外径および肉厚の許容差
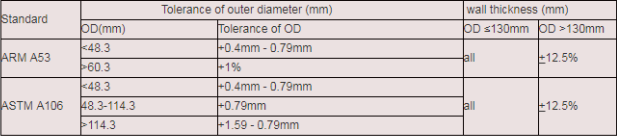
仕様
標準 | 説明 |
ASTM A179/A179M | シームレス冷間引き抜き低合金鋼熱交換器と凝縮器チューブ。 |
API 5L | ラインパイプ。 |
ASTM A53M | 黒&亜鉛メッキ溶接シームレス鋼管。 |
ASTM A106M | 高温用継目無炭素鋼管です。 |
ASTM A105M | 配管用炭素鋼鍛造品。 |
ASTM A234M | 中温および高温での使用に適した鍛錬炭素鋼および合金鋼の配管継手。 |
標準
標準 | パイプの種類 | クラス | 学年 |
APIスペック5L ISO 3183 | SMLS | PLS1 | L245B、L290 X42、L320 X46、L360 X52、 L390 X56、L415 X60、L450 X65、L485 X70 |
PLS2 | L245N BN、L290N X42N、L320N X46N、 L360N X52N、L390N X56N、L415N X60N、 L360Q X52Q、L390Q X56Q、L415Q X60Q、L485Q X70Q | ||
PLS2 サワー環境 | L245NS BNS、L290NS X42NS、L320NS X46NS L360NS X52NS、L390NS X56NS、L415NS X60NS、 L360QS X52QS、L390QS X56QS、L415QS X60QS L485QS X70QS | ||
溶接 | PLS1 | L245B、L290 X42、L320 X46、L360 X52 L390 X56、L415 X60、L450 X65、L485 X70 | |
PLS2 | L245M BM、L290M X42M、L320M X46M、 L360M X52M、L390M X56M、L415M X60M、 L450M X65M、L485M X70M、L555M X80M、 |
標準 | 学年 |
ASTM A 53M | A、B |
ASTM A 106M | A、B、C |
JIS G 3454 | STPG370、STPG410 |
JIS G 3455 | STPG370、STPG410、STPG480 |
JIS G 3456 | STPG370、STPG410、STPG480 |
学年: 化学成分 (%):
標準 | 学年 | C | Si | Mn | P | S | Ni | Cr | Cu | Mo | V |
アストマ 53M | A | ≤0.25 | - | ≤0.95 | ≤0.05 | ≤0.045 | ≤0.40 | ≤0.40 | ≤0.40 | ≤0.15 | ≤0.08 |
B | ≤0.30 | - | ≤1.20 | ≤0.05 | ≤0.045 | ≤0.40 | ≤0.40 | ≤0.40 | ≤0.15 | ≤0.08 | |
ASTM A 106M | A | ≤0.25 | ≥0.10 | 0.27~0.93 | ≤0.035 | ≤0.035 | ≤0.40 | ≤0.40 | ≤0.40 | ≤0.15 | ≤0.08 |
B | ≤0.30 | ≥0.10 | 0.29~1.06 | ≤0.035 | ≤0.035 | ≤0.40 | ≤0.40 | ≤0.40 | ≤0.15 | ≤0.08 | |
C | ≤0.35 | ≥0.10 | 0.29~1.06 | ≤0.035 | ≤0.035 | ≤0.40 | ≤0.40 | ≤0.40 | ≤0.15 | ≤0.08 | |
JIS G 3454 | STPG370 | ≤0.25 | ≤0.35 | 0.30~0.90 | ≤0.040 | ≤0.040 | - | - | - | - | - |
STPG410 | ≤0.30 | ≤0.35 | 0.30~1.00 | ≤0.040 | ≤0.040 | - | - | - | - | - | |
JIS G 3455 | STS370 | ≤0.25 | 0.10~0.35 | 0.30~1.10 | ≤0.035 | ≤0.035 | - | - | - | - | - |
STS410 | ≤0.30 | 0.10~0.35 | 0.30~1.40 | ≤0.035 | ≤0.035 | - | - | - | - | - | |
STS480 | ≤0.33 | 0.10~0.35 | 0.30~1.50 | ≤0.035 | ≤0.035 | - | - | - | - | - | |
JIS G 3456 | STPT370 | ≤0.25 | 0.10~0.35 | 0.30~0.90 | ≤0.035 | ≤0.035 | - | - | - | - | - |
STPT410 | ≤0.30 | 0.10~0.35 | 0.30~1.00 | ≤0.035 | ≤0.035 | - | - | - | - | - | |
STPT480 | ≤0.33 | 0.10~0.35 | 0.30~1.00 | ≤0.035 | ≤0.035 | - | - | - | - | - |
塗装・コーティング
鋼管の表面処理: 石油パイプラインの耐用年数を向上させるために、通常、鋼管と防食コーティングの強固な組み合わせを促進するために表面処理が行われます。一般的な処理方法は次のとおりです: 洗浄、工具の錆取り、酸洗い、ショットブラストの錆取り4つのカテゴリー。
1.洗浄 鋼管の表面に付着したグリース、ゴミ、潤滑剤、有機物などは通常、溶剤、エマルジョンなどを使用して表面を洗浄します。しかし、鋼管表面の錆、酸化皮膜、溶接ノロなどは除去できません。他の処理方法が必要です。 ツール 錆除去 鋼管表面の酸化物、錆、溶接スラグなどをスチールワイヤーブラシを使用して表面処理を洗浄および研磨することができます。
2.工具の除錆は手動と電動に分けられ、手動の場合はSa2レベル、電動工具の場合はSa3レベルに達します。鋼管の表面に特に強い酸化皮膜が付着している場合、除去できない場合があります。工具を使って錆びを取り除くので、他の方法を見つける必要があります。
3.酸洗 一般的な酸洗方法には化学と電気分解が含まれます。ただし、パイプラインの防食には化学酸洗のみが使用されます。化学酸洗は鋼管の表面にある程度の清浄度と粗さを達成することができ、後続のアンカーラインに便利です。通常は再処理後のショット(サンド)。
4.ショットブラストによる錆除去。高出力モーターにより、高速回転刃、スチールグリット、スチールショット、セグメント、鉱物、その他の研磨ワイヤーを遠心力の作用下で鋼管表面にスプレーし、大量に排出し、徹底的に除去します。錆、酸化物、汚れを除去する一方で、激しい衝撃や摩擦力が作用する鋼管を研磨し、必要な均一な粗さを実現します。4つの処理方法の中で、ショットブラストと錆取りは理想的な処理方法です。パイプの錆び取り。一般に、鋼管の内面処理にはショットブラストと錆取りが主に使用され、鋼管の外面処理にはショットブラストと錆取りが主に使用されます。
梱包&積み込み
スプレーペイント
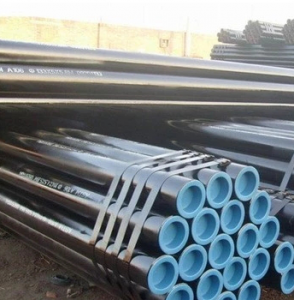
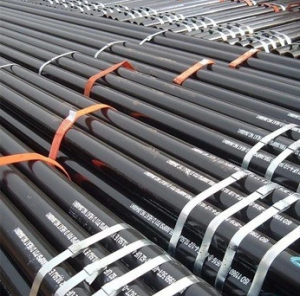
防水梱包
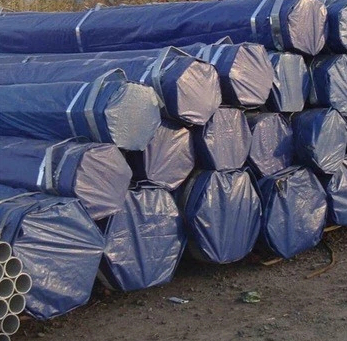